What is the Difference Between Hot Chamber and Cold Chamber Die Casting (Updated)
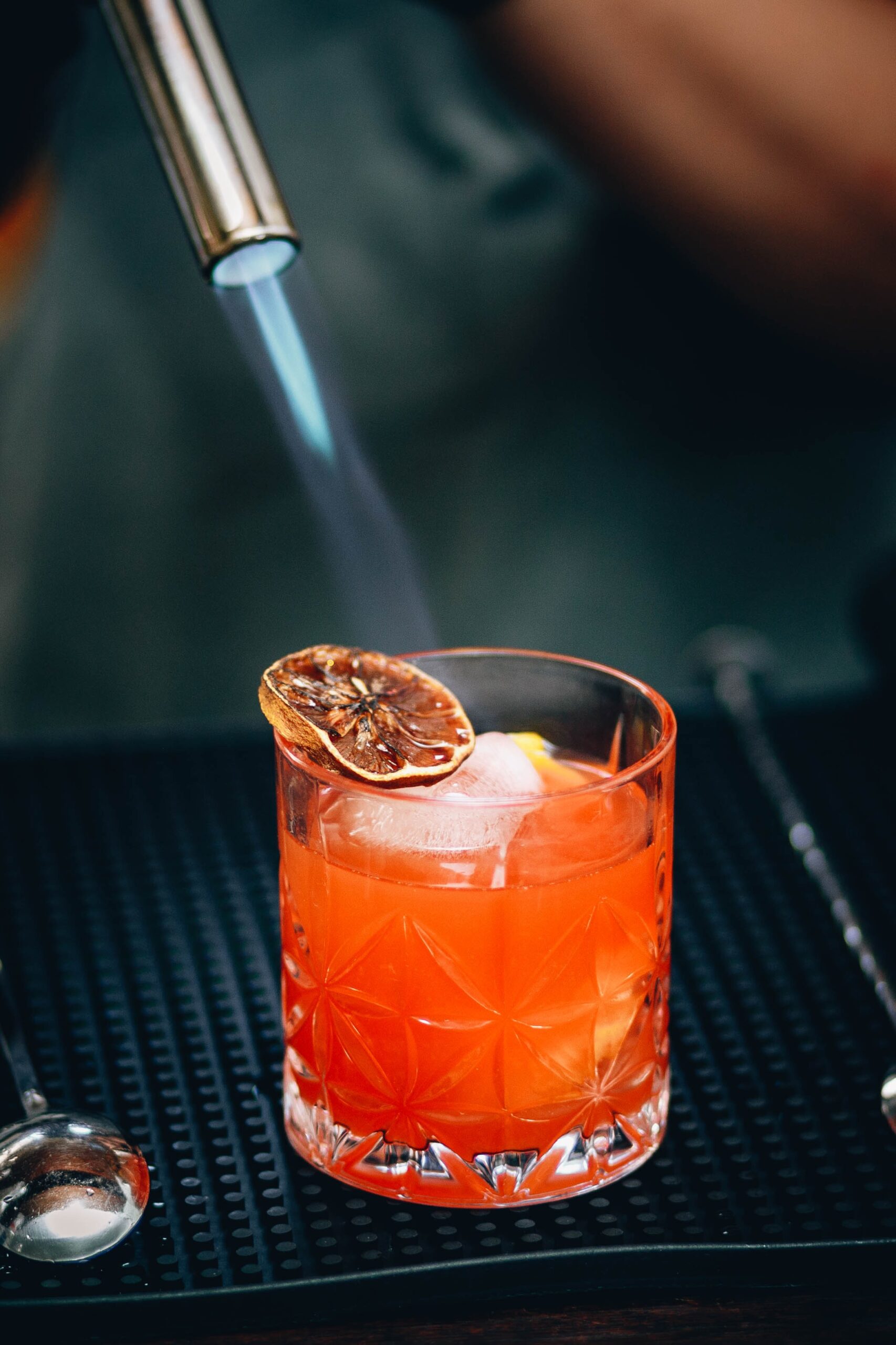
Are you curious about the fascinating world of die casting? Look no further! In today’s blog post, we’ll delve into the intricacies of two commonly used methods: hot chamber and cold chamber die casting. Whether you’re a manufacturing enthusiast or simply seeking to expand your knowledge, join us as we unravel the differences between these two techniques and discover how they shape the products that surround us every day. Get ready for an illuminating journey into the captivating realm of die casting!
The Process of Hot Chamber Die Casting
Explanation of Hot Chamber Die Casting Process
Hot chamber die casting is a widely adopted manufacturing process for creating intricate and precise metal components, especially for materials with low melting points like zinc and magnesium. The process involves the use of a die made of two steel halves, molten metal injection under pressure, and the rapid solidification of the metal within the die cavity. The result is a fully formed metal part with a polished finish, and the efficiency of hot chamber die casting lies in its minimal downtime between injections due to the constant heating of the molten metal.
However, there are limitations to consider, including the restriction to materials with low melting points and the potential for a shorter tool life due to direct contact between the molten metal and components like pistons. Despite these limitations, hot chamber die casting finds applications in various industries, such as automotive manufacturing, consumer electronics, and appliance production.
Advantages and Disadvantages
Advantages of Hot Chamber Die Casting
- Rapid production with minimal scrap material, leading to cost savings and faster turnaround times.
- Capable of crafting complex shapes with exceptional precision and meeting tight tolerances.
- Excellent surface finish, making it suitable for products in industries where aesthetics are important, such as automotive, aerospace, and consumer electronics.
Disadvantages of Hot Chamber Die Casting
- Limited range of materials it can handle, typically restricted to alloys with low melting points like zinc or magnesium.
- Challenges in handling large-sized parts due to machine size and pressure constraints.
For larger components or materials with higher melting points like aluminum or copper alloys, cold chamber die casting may be a more suitable alternative.
Applications in Industries
Hot chamber die casting is a widely used method in industries with high production volumes and intricate designs, including automotive, aerospace, electronics, and consumer goods. In automotive manufacturing, it is crucial for precise components like engine blocks and transmission cases, to offer excellent surface finish and accuracy. Aerospace relies on it for lightweight yet robust parts such as turbine blades and engine housings.
The electronics industry benefits from its ability to create intricate designs with durability and heat dissipation properties. In consumer goods production, hot chamber die casting is cost-effective and ensures high-quality products. Its popularity in these industries arises from its efficiency in crafting complex shapes with precision.
The Process of Cold Chamber Die Casting
Explanation of Cold Chamber Die Casting Process
Cold chamber die casting is a precise manufacturing method for high-quality metal parts. Molten metal is introduced into a cold chamber or shot sleeve and propelled into the die cavity under high pressure through hydraulic or mechanical means. The preheated die ensures it can withstand extreme temperatures, and precise control over filling speed and pressure is achieved by ladling the molten metal into the shot sleeve and injecting it with a piston or plunger.
In contrast to hot chamber die casting limited to low-melting-point alloys, cold chamber die casting accommodates a broader range of materials, including aluminum, magnesium, copper, and zinc-based alloys, making it suitable for parts requiring higher strength and durability. Notably, it can manufacture larger and more intricate parts compared to hot chamber die casting, and the separation of melting and injection chambers eliminates potential alloy contamination issues.
Advantages and Disadvantages
Advantages
- Speed and Precision: Hot chamber die casting allows for rapid production of complex shapes with high precision.
- Efficiency: Continuous replenishment of molten metal enables uninterrupted operation, leading to higher productivity and reduced downtime.
- Surface Finish and Accuracy: The process ensures excellent surface finish and dimensional accuracy, making it ideal for applications with aesthetic and tight tolerance requirements.
Disadvantages
- Limited Material Compatibility: Hot chamber die casting is restricted to low melting point metals like zinc and magnesium, limiting its suitability for applications requiring stronger materials.
- Gooseneck Tube Vulnerability: The use of a gooseneck tube exposes the process to potential corrosion over time, necessitating regular maintenance and replacement for consistent performance.
Applications in Industries
The cold chamber die casting process involves the precise crafting of high-quality metal parts. Molten metal is introduced into a cold chamber and pushed into a die cavity using hydraulic or mechanical pressure. Preheating the die ensures it can withstand high temperatures.
Unlike hot chamber die casting, which is limited to low-melting-point alloys, cold chamber die casting accommodates a wider range of materials like aluminum, magnesium, copper, and zinc-based alloys, making it ideal for durable parts. A key benefit is the ability to create larger, complex parts compared to hot chamber die casting while avoiding alloy contamination due to separate melting and injection chambers. However, it has a slower cycle time due to die preheating.
Comparison Between Hot Chamber and Cold Chamber Die Casting
- Hot Chamber and Cold Chamber Die Casting are distinct methods for manufacturing high-quality metal parts, each with its unique process and suitability.
- Hot Chamber Die Casting immerses the injection mechanism in molten metal, enabling faster cycle times. It’s ideal for materials with low melting points like zinc and magnesium alloys.
- Cold Chamber Die Casting involves a separate furnace to melt the metal before injecting it into the mold. This is suitable for metals with higher melting points like aluminum and copper alloys, albeit with longer cycle times.
- Choosing between the two depends on your specific needs. The hot chamber is cost-effective for small-scale production with shorter cycle times, while the cold chamber provides flexibility in material selection, strength, and durability for metals with higher melting points.
The choice should align with your project requirements, and expert guidance is crucial to make an informed decision that suits your manufacturing goals.
Factors to Consider When Choosing Between Hot Chamber and Cold Chamber Die Casting
When deciding between hot chamber and cold chamber die casting, several crucial considerations come into play. Each method has its distinct advantages and limitations, necessitating a careful assessment based on your specific needs.
- Material Type: Hot chamber die casting is ideal for low-melting-point materials like zinc and magnesium alloys, while cold chamber die casting is better suited for high-melting-point materials such as aluminum or brass.
- Production Volume: Hot chamber die casting is more efficient for high-volume production due to faster cycle times, while cold chamber die casting is better for lower volume runs.
- Part Complexity: Hot chamber die casting excels in crafting intricate parts with thin walls and complex geometries, while cold chamber die casting may be preferable for parts with thicker walls or challenging characteristics.
- Cost Considerations: While cold chamber die casting may have higher initial equipment costs due to the need for additional machinery, it can offer savings in tooling life and maintenance.
- Operator Safety: Operator safety is a important factor. Hot chamber die casting involves continuous exposure to molten metal, which can be hazardous without proper training. In contrast, cold chamber machines provide an extra layer of protection as operators don’t have direct contact with molten metal during operation.
By carefully evaluating these factors, you can make an informed choice between hot chamber and cold chamber die casting methods that align with your specific manufacturing requirements.